Key Advantages and Factors To Consider of Applying Plastic Extrusion in Your Projects
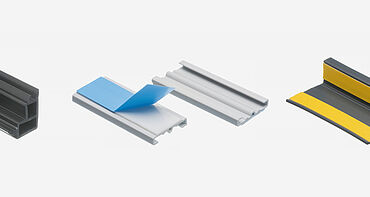
Understanding the Fundamentals of Plastic Extrusion
Plastic extrusion, a staple in the manufacturing sector, is a procedure that includes melting raw plastic material and improving it right into a continual account. This profile, once cooled down, can be reduced into desired lengths or curled for later usage. The appeal of plastic extrusion lies in its adaptability. A wide variety of products, from piping to home window structures, can be generated. The process calls for an extruder, a complex equipment with a heated barrel, a turning screw, and a die at the end. The plastic product, in the form of pellets, is fed into the extruder, where it's melted and required through the die, taking its shape. The choice of plastic and the style of the die determine the item's characteristics.
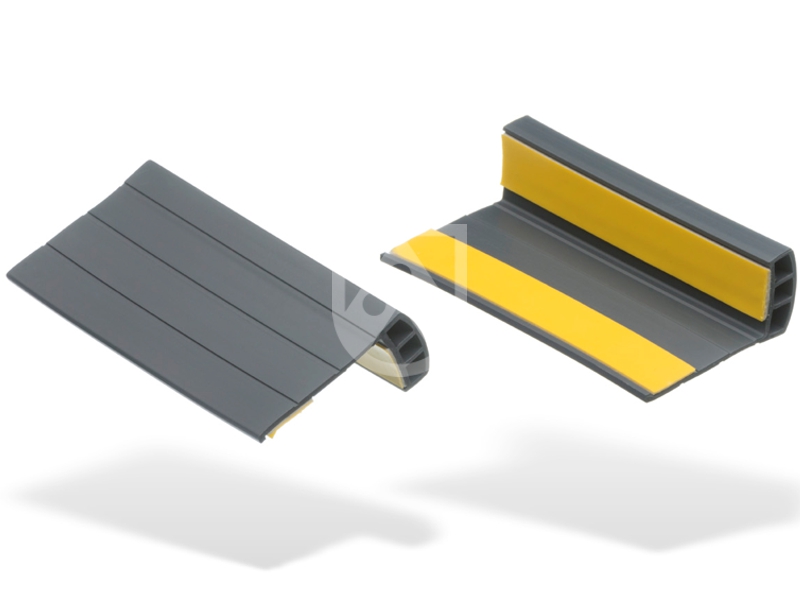
The Economic Advantage of Plastic Extrusion
The financial advantage of plastic extrusion lies predominantly in 2 locations: affordable product production and valuable production rates. With plastic extrusion, companies can generate high quantities of material at a reduced expense contrasted to other approaches. The process boasts an outstanding manufacturing rate, dramatically reducing time and further improving its economic stability.
Cost-Effective Material Manufacturing
A significant benefit of plastic extrusion is its exceptional cost-effectiveness. This production procedure permits for continuous, high-volume production with minimal waste, which equates into reduced expenses. The raw products utilized, commonly plastic pellets, are relatively economical compared to other compounds (plastic extrusion). The procedure itself calls for much less power than several various other manufacturing approaches, additionally reducing costs. Furthermore, the extrusion process enables a high level of accuracy in forming the plastic, minimizing the requirement for expensive post-production modifications or adjustments. The longevity and longevity of extruded plastic products typically indicate less need for replacements, contributing to lasting financial savings. All these aspects make plastic extrusion an extremely cost-effective choice for many tasks, offering an attractive balance in between expense and performance.
Beneficial Manufacturing Speeds
While keeping the cost-effectiveness of the products, another noteworthy benefit of plastic extrusion exists in its quick manufacturing speeds. This efficiency in the production procedure is credited to the continual nature of the extrusion procedure, permitting for high-volume manufacturing in a fairly short time period. The speed of production straight associates to a reduction in labor prices and an increase in output, consequently boosting the overall economic feasibility of the procedure. Additionally, the hectic manufacturing does not endanger the quality of the final item, guaranteeing constant and dependable outcomes. This mix of rate, top quality, and cost-effectiveness underscores the significant financial benefit of executing plastic extrusion in different jobs.
Versatility and Customization: The Strengths of Plastic Extrusion
One of the popular strengths of plastic extrusion hinges on its convenience and personalization capacity. These high qualities open the door to endless layout possibilities, giving suppliers the capacity to customize products to particular needs. This enhanced level of personalization not only enhances product functionality yet likewise dramatically improves product originality.
Unrestricted Style Opportunities
Plastic extrusion beams in its capability to provide almost limitless style possibilities. This method gives flexibility to develop complicated forms and elaborate accounts, a task difficult to attain with other fabrication methods. Owing to the fluid nature of liquified plastic, the process is flexible sufficient to produce a varied variety of kinds, dimensions, and measurements. The plastic can be controlled to match one-of-a-kind specs, permitting for the manufacturing of personalized geometries and meeting specific client needs. Plastic extrusion can handle a variety of plastic types, increasing its application scope. This adaptable technique, consequently, serves a variety of industries from building to auto, product packaging to electronics, and beyond. With plastic extrusion, the design possibilities are basically endless.
Increasing Item Individuality
The flexibility of plastic extrusion can substantially boost item uniqueness. This process enables designers to experiment with various forms, dimensions, and shades, providing them the flexibility to produce distinct products that stand out on the market. It is this customization that lends a distinctive find out identification per product, identifying it from its rivals.
In enhancement to its aesthetic benefits, the customizability of plastic extrusion additionally uses useful benefits. Developers can modify the buildings of the plastic according to the details requirements of the application, enhancing the item's performance. For example, they can make the plastic extra versatile, Visit Your URL much more sturdy, or extra immune to warm, relying on what the item needs. Therefore, plastic extrusion not just improves product originality but likewise its utility and bankability.
Layout Limitations in Plastic Extrusion: What You Need to Know
Just how can create limitations possibly affect the procedure of plastic extrusion? While plastic extrusion is functional, style constraints can reduce its benefits. Certain complicated layouts might not be possible as a result of the restrictions of the extrusion process, potentially limiting the creation of elaborate accounts. The procedure is less suitable for multi-chambered or hollow structures. In addition, the extrusion process may not constantly give the desired surface finish, especially for those calling for high gloss or optical quality. Material selection can likewise present obstacles, as not all polymers appropriate for extrusion. High-temperature resistant plastics, for example, may provide problems. Recognizing these constraints is vital for effective implementation of plastic extrusion in your tasks. plastic extrusion.
Examining the Ecological Influence of Plastic Extrusion
While recognizing style limitations is a significant aspect of plastic extrusion, it is just as vital to consider its ecological ramifications. The process of plastic extrusion involves melting plastic products, possibly releasing unsafe gases into the setting. Using recycled plastic materials in the extrusion procedure can minimize ecological effect.
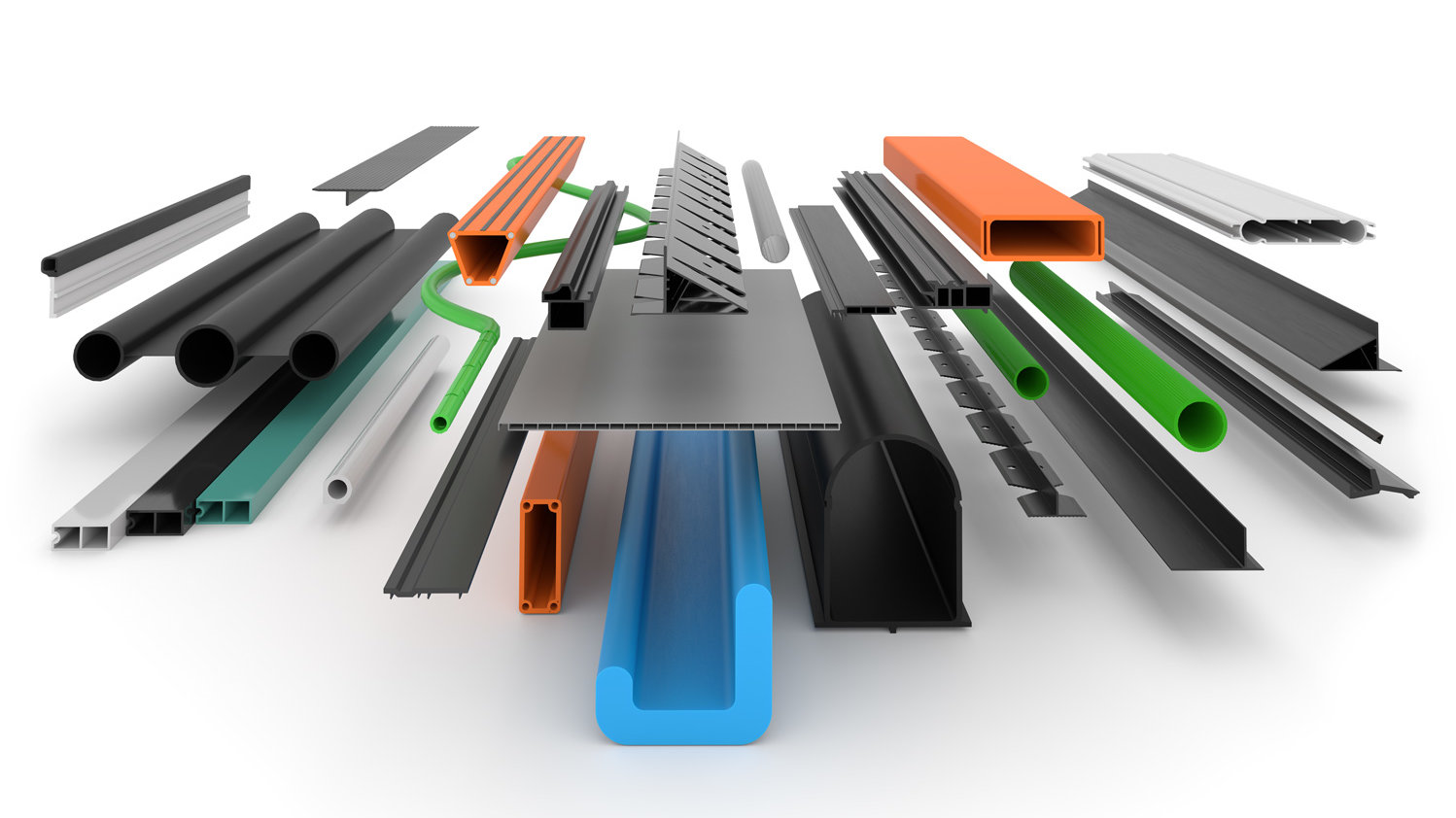
Instance Study: Successful Projects Utilizing Plastic Extrusion
Success tales in the field of plastic extrusion abound, demonstrating both the flexibility and efficiency of this production procedure. One notable example is the creation of PVC pipelines made use of in modern plumbing. This procedure involves melting plastic and forming it into a continuous tube, using substantial price and durability advantages. Another successful case is the production of plastic movie for product packaging and farming. With extrusion, makers can create extremely adjustable, thin, and robust movies. Automotive sectors additionally benefit, utilizing extruded plastic for parts like trim or seals, enhancing vehicle longevity. These circumstances highlight plastic extrusion's crucial function in different markets, testifying to its flexibility, cost-effectiveness, and dependable outcome.
Final thought
In conclusion, plastic extrusion supplies a cost-effective and efficient technique for producing complicated shapes with very little waste. While it provides many advantages such as cost-effectiveness and convenience, it's important directory to consider prospective layout restrictions and ecological impacts. Applying biodegradable or recycled products can mitigate these concerns, enhancing sustainability. Including plastic extrusion into projects can cause successful end results, as confirmed by countless situation studies.
Plastic extrusion, a staple in the manufacturing market, is a process that includes melting raw plastic product and improving it right into a continual profile. Plastic extrusion can deal with a range of plastic kinds, expanding its application scope.How can create constraints potentially impact the process of plastic extrusion? The process of plastic extrusion entails melting plastic materials, potentially launching damaging gases right into the atmosphere. Using recycled plastic materials in the extrusion procedure can lower environmental effect.
Comments on “Why plastic extrusion is perfect for mass production”